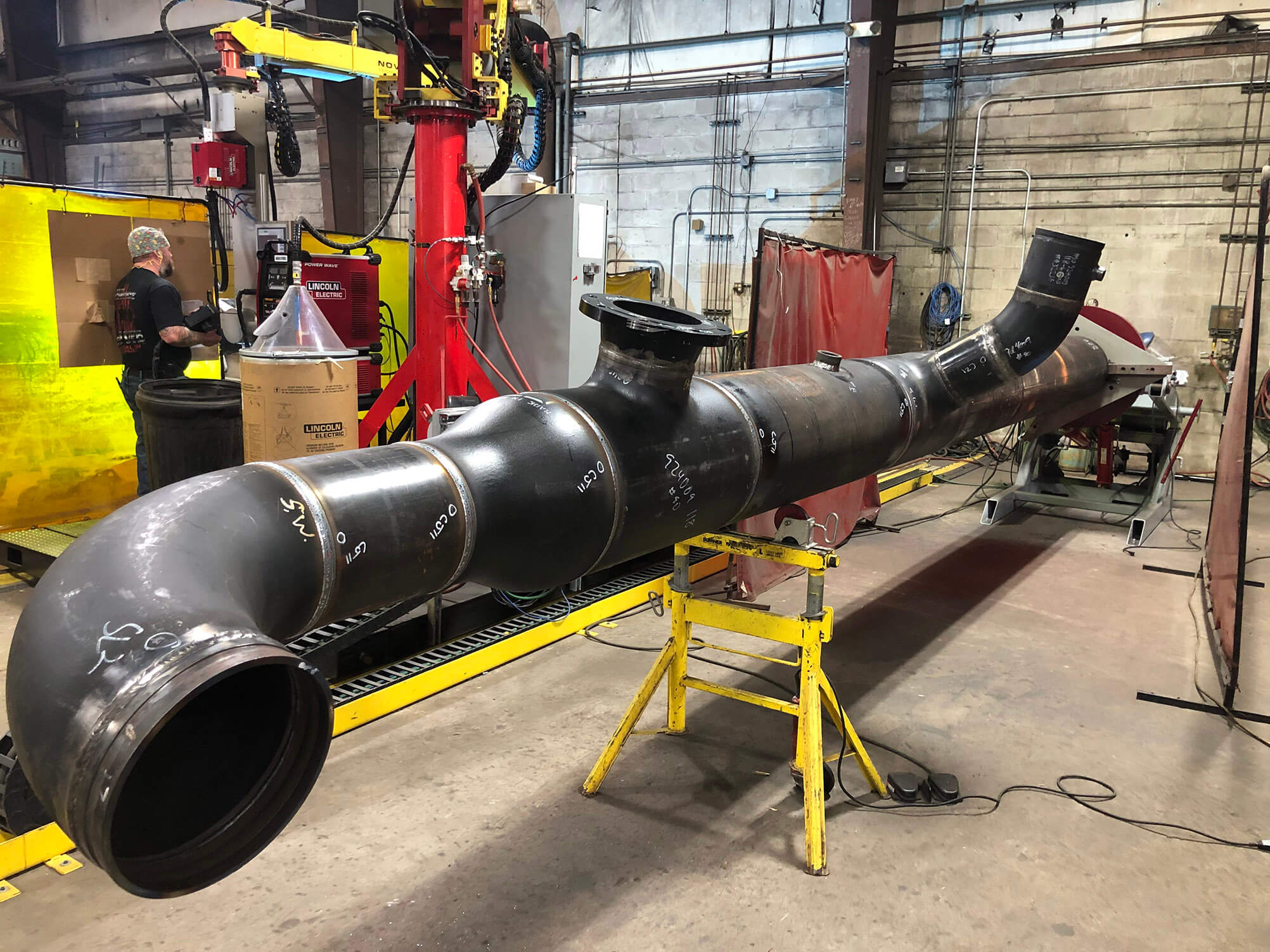
W.W. Gay Mechanical Contractor, Inc. saw a 200-percent increase in shop productivity and a 12-fold increase in weld productivity by implementing Novarc Technologies Inc.’s collaborative Spool Welding Robot (SWR). They are also realizing a 100-percent pass rate on radiography tests (RTs). The SWR has reduced W.W. Gay’s dependence on highly skilled welders, of whom there is a global shortage.
Based in Florida, W.W. Gay provides a variety of commercial and industrial contracting services, and has the experience, equipment, facilities, and professional licensures and certifications to meet even the largest project requirements. To maintain their competitive edge, they needed to increase their productivity and efficiency to keep up with the fast-track projects in their market while ensuring high quality. W.W. Gay sought an automated welding solution that would allow them to use junior welders for simpler work and deploy their more experienced welders on other key projects.
Collaborative Solution
David Ray, W.W. Gay’s pipe fabrication shop foreman, explained, “We looked extensively to find a solution, and we narrowed our search to several companies. After putting all our choices under the microscope, it was an easy choice. Only the Novarc SWR has the capabilities to do what we do on a daily basis in our shop.” The SWR is designed specifically for pipe, small-pressure vessel, and other types of roll welding.
The company implemented the SWR at their facility and trained their operators to use it. Using the SWR combats the shortage of highly qualified welders because it can be operated by less-experienced workers and produce high-quality welds every time.
Ray continued, “My first impression was that the SWR was a really good investment. My impression now is that my first impression was 100-percent accurate.”
Ray also appreciated Novarc’s responsiveness. “To date, any question or suggestion I have made has been met with a quick response, and we are 100-percent happy that we chose the Novarc SWR,” he said. “The SWR was the only solution out there that fit our needs, it was a perfect fit.”
Productivity Soars
Before purchasing the SWR, the team at W.W. Gay was welding between 80 and 100 diameter-inches on average per shift using welding positioners with the gas metal arc welding and flux core arc welding processes. The company wanted to increase the welding bays’ inch count to the maximum amount that they could imagine.
“With the SWR, we have seen a tremendous increase of weld inches per shift from 6” and bigger,” Ray noted. “Depending on pipe size, we can hit inch counts anywhere from 200” to 275” on a regular basis with the SWR.
“The fact that we can weld slip on flanges is probably one of the most impressive tasks that the Novarc SWR is capable of,” Ray continued. “Also, we have gotten really efficient at welding stainless steel fabrication with the SWR, and this is helping tremendously with our efficiency. Our old way of welding stainless would be to TIG [tungsten inert gas] weld with using an ID [inner diameter] purge. A 16” schedule-10 weld would take two-and-a-half hours or so to get a purge set up and then weld out. We now can do a 16” schedule-10 weld in 12 minutes that will pass RT.” said Ray.
Quality Improves
The SWR minimizes human error and therefore reduces the failure rate from the industry average of 3–5 percent to less than 1 percent. Ray noted, “The thing about the SWR is that it is a start-to-finish weld—once you hit the ‘go’ button, it welds the root, fills, and cap without stopping, which makes doing a weld that has to be RT’d a bit of a cakewalk, since there is no in-between pass clean up and prep. We currently have a 100-percent pass rate with our RTs on the SWR. To put this into perspective, a 10” standard-weight weld can be achieved in 12 minutes or so, which is highly remarkable.”
Managing the Welder Labor Shortage
With the SWR, W.W. Gay can assign their highly skilled welders where they are most needed. The company currently has three trained SWR operators, including a third-year apprentice, who are all equally efficient with running the SWR.
“[The SWR] is head-and-shoulders better and more efficient, and the quality is amazing,” observed Jason Craven, welder at W.W. Gay. “I’m completely comfortable using it, there are no problems at all. Once you get the hang of it, it is easy to use. … [Novarc] provided excellent training.”
Ray pointed out that the SWR opens up opportunities for W.W. Gay. “We do our shop tours for any specific general contractor that we may be working for,” said Ray. “They are really impressed when they see the speed and precision of the SWR. And when I explain how the SWR has improved our efficiency, it is a major eye-opener at our capabilities to keep up with job flow needs and expectations.”
Novarc’s podcast series tackles topics such as the impact of automation on manufacturing. Listen here: https://www.novarctech.com/resources/podcasts/
For more information, visit www.novarctech.com.